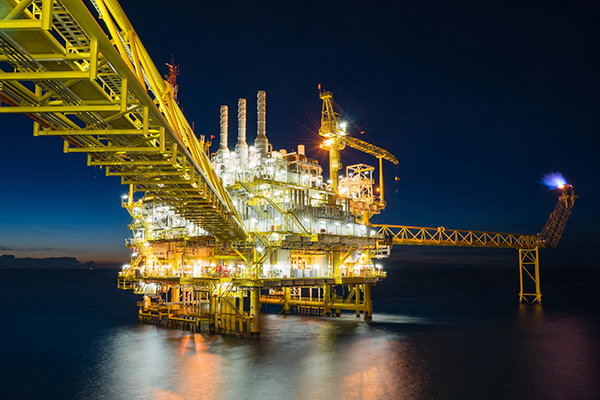
A global oil & gas producer with more than 50 production sites and 80,000 employees spread across 5 continents around the world.
The Problem
This company is a long-time user of the Apollo Root Cause Analysis methodology. Their North American Reliability Engineering and Maintenance team has trained more than 200 people in the method and completed between 200-300 RCA investigations over the last decade.
They had amassed a large database of RCAs, but had no central place to store them and no good way to search the information contained within them.
Solution
The company decided it was time for an enterprise tool that would consolidate and house all their RCA files from their more than 30 North American sites in one central, cloud-based location. RC Pro™ fit the bill, offering a comprehensive, web-based database where the company could securely store all the information related to their RCAs - solutions, causes, equipment types, photos, internal resources, reports, and more. They did a mass migration of all their RCA files into the RC Pro™ system, being careful to tag and classify those past RCAs so all of the information would be highly searchable.
Deeper Data Mining, Improved Solutions
RC Pro™ gave the company greater data mining capabilities than they'd ever had before. They were able to pull reports that showed them very specific information, such as which equipment types were most associated with failures. RC Pro™ generated charts showing clearly that their rotating equipment (specifically pumps) was experiencing far and away more issues than anything else-almost twice as many failures as the next most problematic type of equipment. (Figure 1&2) This helped them to prioritize the areas that needed further investigation and resources, and to take corrective actions that would result in the greatest reduction of future events.
Through the use of this data, weaknesses in the existing PM program were identified and it was found that more than 30 percent of the solutions were related to FMEA/RCM. This enables corrective actions to be taken not only in this instance but also to enable system wide improvement in processes.
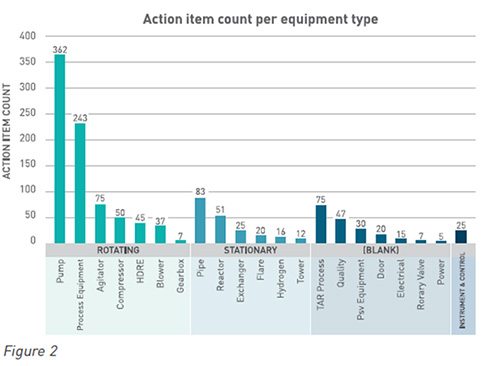
More Visible, Permanent Knowledge-Base
In addition to more constructive use of the data, the company is also benefiting from greater accessibility to the data across its many sites. Now when an event occurs, a team member can search across the database to see if a similar event has happened at another site, quickly finding out the details of the investigation and who was involved. It gives them a significant head start. Additionally, if any team members leave the company, that institutional knowledge doesn't walk out the door along with them - all the details of the investigation live forever within the database. Team members can easily share files within the system, uploading evidence and data to RC Pro™.
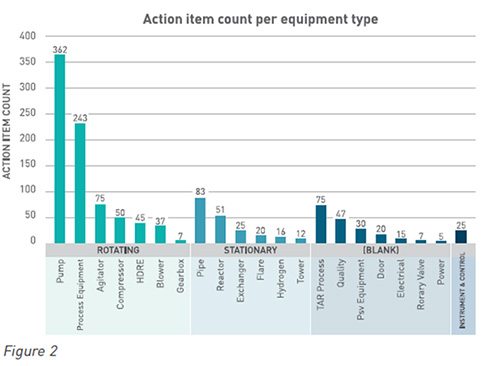
The Outcome
If the company summed up all of the benefits they've seen using RC Pro™ into one word, it would be visibility. They now have far greater insight into their biggest problem areas and can be more specific in pinpointing causes and more comprehensive in their solutions. They can also see which teams are having the most success and determine how to duplicate it. Team members have more visibility into what's happened at other sites and can take advantage of lessons learned elsewhere rather than re-inventing the wheel. It's like having their own company-specific RCA Wikipedia-all the knowledge and resources their RCA program has amassed over the years is just a quick search away.