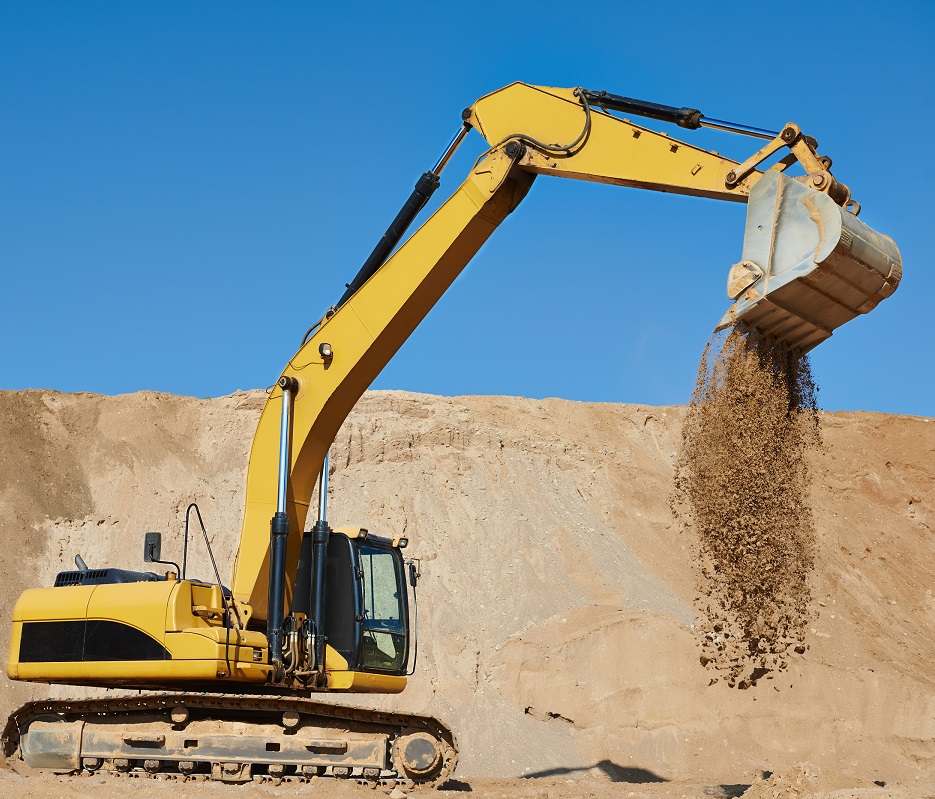
Executive Summary
The Barrick Gold Pueblo Viejo Mine Development is located in the Dominican Republic, approximately 100 kilometers northwest of the capital city of Santo Domingo. At the time of ARMS' engagement at the Pueblo Viejo mine, the project was advancing in line with its $3.0 billion capital budget, with the construction of the mine nearing completion and commissioning already commenced in various areas of the mine. The mine was at that time currently forecasting 23.7 million ounces of reserves resulting in an expected mine life of over 25 years.
With the mine development nearing completion, the project team had the goal of having a complete asset strategy in place prior to the start of operations. This meant ensuring the introduction of a robust and justifiable maintenance strategy that included both predictive and preventive tasks ready for deployment and upload into Oracle EAM.
The project team engaged ARMS Reliability to expedite the process, in part due to ARMS' proven RCM expertise and previous experience completing similar studies for mining clients such as BHP Billiton.
To meet Barrick's objectives, ARMS Reliability
- Worked closely with the Barrick Gold - Pueblo Viejo project team, OEM's, and subject matter experts to collect the most helpful project data
- Used ARMS Reliability’s extensive project library to provide failure data where site personnel did not have experience or OEM information did not exist
- Used this data to develop optimum maintenance plans and predict budgets, resource requirements, and total lifetime costs.
- Wrote work instructions to support the selected maintenance tasks and downloaded them to templates, ensuring standardization and the ability to easily update.
As a result, Barrick Gold Pueblo Viejo had robust, justifiable equipment strategies that were developed within the context of overall expected plant performance which could be shared with similar Barrick facilities worldwide.
The Challenge
Barrick Gold - Pueblo Viejo had 3 main objectives:
- Development of Preventive Maintenance Instructions (PMI)'s that added value to the business
- Review OEM recommendations, and provide a scientific approach for justifying the frequency of PMs
- Ensure participation from all PVDC maintenance and operations sections
The project team viewed this initial study as a curtain raiser to the future of its preventive maintenance program. Over the coming operational years, the strategy would be groomed to better suit the plant needs. For example, PMs would be amended, work instructions updated, frequencies refined against failure information, addition of tasks etc.
The Solution
The ARMS Reliability approach is to develop a FMEA structure which identifies the likely failure modes for each asset and describes maintenance tasks to address them. Using reliability modeling ARMS is able to develop optimum maintenance plans, predict budgets, resource requirements, and total lifetime costs. Maintenance tasks are described and estimates for labor, materials and equipment are assigned. The optimum type of task (Run to Fail, Preventive, Inspection, Monitoring, Commissioning or Redesign) is chosen. The optimum interval between tasks is also established, and task groups defined to ensure resource efficiency and minimal planned downtime. This step is the decision making phase of the Maintenance Plan Development and where the ARMS Reliability facilitator involves operators and maintainers of the equipment.
ARMS Reliability worked closely with the Barrick Gold - Pueblo Viejo project team, OEM's and subject matter experts to collect the most helpful project data. ARMS Reliability also called upon an extensive project library to help populate various equipment items with pre-populated failure information, where site personnel did not have experience or OEM information did not exist.
In 8 months, ARMS Reliability developed approximately 500 maintenance plans for 2770 assets which covered nearly 50% of the Pueblo Viejo facility. Following the creation of the maintenance plans,work instructions to support the maintenance tasks identified in the maintenance strategy were written. The ARMS Reliability solution has the ability to produce large amounts of documentation whereby job instructions that are directly written in the strategy selection tool are downloaded to templates thus ensuring standardization of the maintenance plan and job instructions which can be easily updated.
"We saved a large amount of time by using reliability modeling software to manage the process. Plus, having a facilitator ensures that there is someone dedicated to the process who is unencumbered."
Project Deliverables
- Detailed RCM models for equipment
- Developed a Functional Asset Hierarchy
- FMEA Drilldown (Can be used to set failure reporting codes)
- Maintenance Plans for upload to CMMS system
- Work instruction documents conforming to a Barrick template
- Zero based maintenance budget predictions
- Labor resource predictions
- Spares usage predictions
- FMEA & FMECA reports
- Identification of high risk failure modes
- Equipment Criticality based on defined thresholds
Besides the tangible benefits listed above, additional fringe benefits arose as a result of involving the operation and maintenance teams early in the process. The personnel gained an early understanding of the equipment and processes they would eventually control. In addition, it gave them the opportunity to meet and become familiar with some of the equipment suppliers and representatives, helping to build the relationships that are essential to reliable plant operation.
The Benefits
Benefits Barrick Gold Pueblo Viejo identified some key advantages of using Reliability Modeling tools for improving asset management plans:
- It provides Barrick Gold with a valuable means of educating the operators and maintainers in what the critical areas require to ensure high levels of plant availability.
- It provides a systematic process of knowledge capture that can be challenged and updated over the life of the plant.
- Barrick Gold Pueblo Viejo knows that individual equipment, failures and maintenance actions are seen in context of overall plant performance.
- Barrick was able to gain enhanced knowledge of the new plant. As new people were introduced to the site, the RCM process was used to gather their knowledge and information, as well as serving as communication tool for the project team to explain the chosen strategy
- The approach taken ensures the maintenance plans are consistent with the expected system performance and design objective.
- Partnering with ARMS Reliability enabled Barrick to increase the capabilities of its team and meet necessary training regulations by training the team in the technology and techniques
- The generation of a standard set of asset strategies which can be shared with similar Barrick facilities worldwide
- Data that is collected in the future can be plugged into the simulation tools to create updated models and revised strategies.
- Barrick is now equipped with tools it can use to generate long-term results
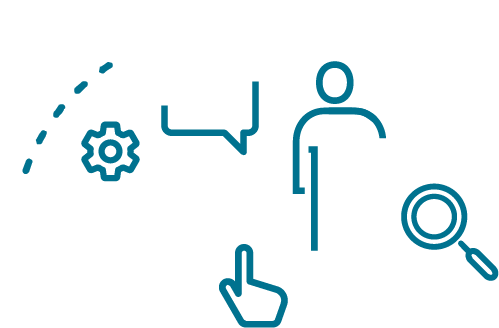
Questions? We'll put you on the right path.
Ask about our Maintenance Strategy Development services and technical solutions. We are ready to help.
Contact Us