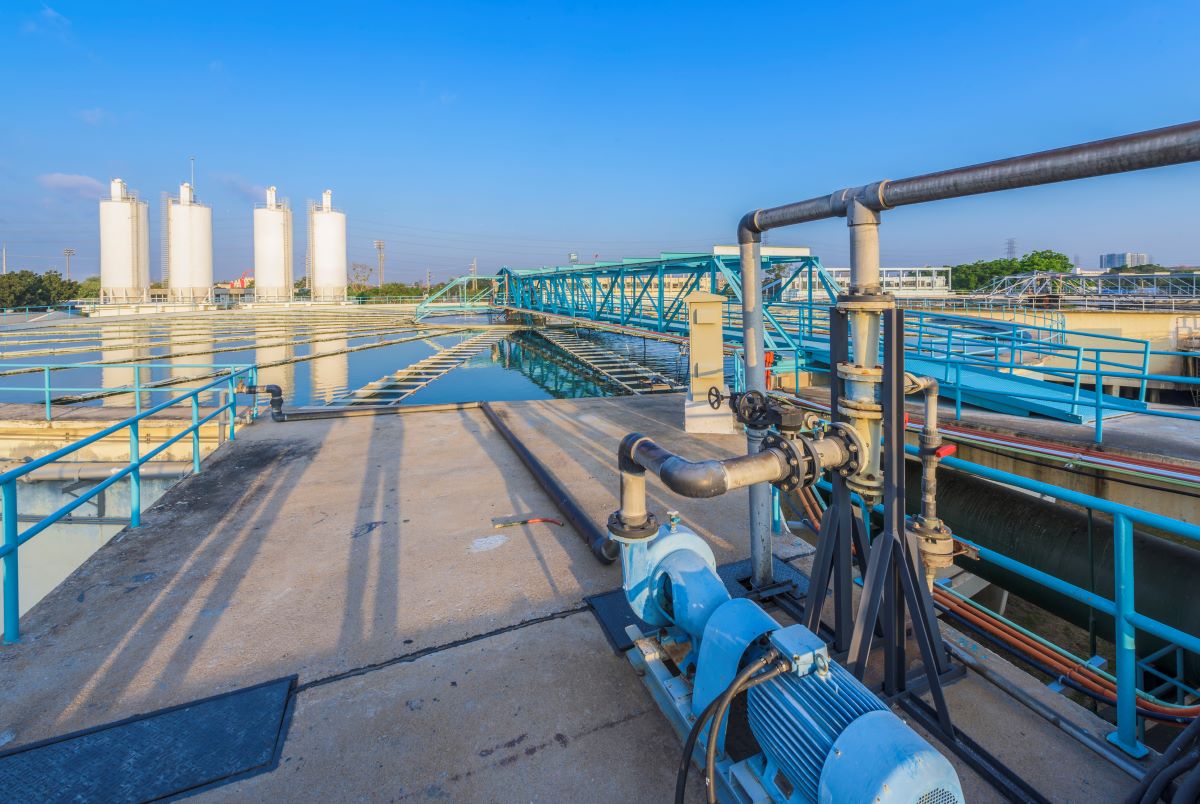
Executive Summary
Icon Water supplies essential water and sewerage services to the Australian Capital Territory (ACT). It has served the community for more than 100 years and sources, treats and supplies water through a direct relationship with its customers.
Today, Icon Water owns and operates assets worth over $2.2 billion, comprising the ACT’s network of dams, water treatment plants, sewage treatment plants, reservoirs, water and sewage pumping stations, mains, and other related infrastructure. As a regulated utility, it has a responsibility to ensure effective asset management and provide the right balance of cost and performance for ratepayers.
To meet these obligations and adopt a leading Practice approach in line with the ISO 55000 standard, Icon Water made the decision to transition to a new Oracle EAM system and revolutionize their entire approach to asset management. The step change involved developing new asset strategies for 700,000 assets and loading them into Icon Water’s Oracle Works Asset Management System (WAM).
In order to get this mammoth task done right and on time, Icon Water engaged ARMS Reliability and used its Asset Strategy Management (ASM) system, Cordant™ Asset Strategy. The ARMS team were engaged for all three aspects of asset management (build, deploy and sustain).
From behind the curve to leading practice
The company relied on very knowledgeable personnel executing maintenance activities built up from experience. Execution crews were accountable for planned and reactive work and justification for maintenance was not documented or linked to the asset’s function. Asset criticality analysis had not been completed and the existing EAM system had reached end of life.
Rather than work through this long list of improvement opportunities one by one, Icon Water adopted a “big bang” approach to reliability and work management improvement. It adopted the Oracle EAM and WAM systems and set to work developing strategies for its 700,000 assets.
The work was complex and time consuming and while Icon Water managed to build out 60% of its asset strategies on its own, it decided it could not complete the project on time and in a sustainable manner without an ASM system. “We had 600 individual spreadsheets to capture our asset strategies and to control and amend that was becoming a nightmare. What really tipped us over the edge though was the idea of taking all of these individual sheets and turning them into work orders. I’ve implemented an ASM system before, and I knew that using one of these systems was the smart way to go,” said Andrew Behn, Maintenance Planning and Reliability Team Lead at Icon Water.
The team at Icon Water met with ARMS Reliability and found OnePM an ideal solution to accelerate the process of packaging and loading corrective work orders into the WAM. With its component strategy library, the solution would also help the team with the 40% of asset strategies still to be completed.
Additionally, OnePM would help Icon Water meet its wider reliability goals with a leading Practice approach to ASM by setting the foundations for a sustainable reliability culture.
Rapid development and deployment of strategies
At the point Icon Water engaged with ARMS Reliability, it had less than six months to build its remaining strategies and then package and load all work orders. To meet this timeframe, the company had experts from ARMS Reliability come in and work alongside its planners to develop strategies and ensure the most efficient approach for packaging work orders.
Augmenting their existing strategy data with the OnePM component strategy library, they were able to quickly develop strategies based on information like asset type, duty, process, criticality and environment, and then optimize these in line with Icon Water’s reliability goals and operating environment. There are owners for each strategy so that if there is a failure in one of Icon Water’s 28,000 valves for example, the strategy can go back to the owner for review and they can quickly assess if that failure could impact the other 27,999 valves. If the answer is yes, they can put a new control into the strategy and roll it out to all of the assets instantaneously.
“We couldn’t have finalized our strategies in time to meet with the aggressive timeline for the EAM implementation without working with ARMS Reliability and using the OnePM System. Also, now our strategies are designed in a way that if we identify one defect, we can knock out many and avoid future failures. This is helping us move from a reactive culture of Defect Elimination to a more proactive culture of Defect Prevention,” said Andrew.
Once strategies were complete, Icon Water worked alongside ARMS Reliability to set up rules for work packaging in OnePM. For example, they were able to establish guidelines on how and when work, like valve maintenance, needed to be performed and whether the work required plant or equipment to be in isolation.
By applying these rules to the asset strategies, Icon Water was able to automatically package work orders and then review and refine. This avoided a huge amount of manual effort and ultimately allowed Icon Water to meet its project timelines.
Andrew said the use of OnePM had also helped Icon Water adopt a standard look and feel for work orders and made it much easier to adjust strategies and work orders in the future. “Going forward, if we need to make a change to an asset maintenance plan, we can repackage the work order at the press of a button,” he said.
A new culture of Reliability
Complementing the delivery of OnePM and new asset strategies and work orders for Icon Water’s assets is clearer ownership and accountability for asset reliability. Planners are responsible for the cost and performance of assets and work with strategy owners to address failures and customize strategies as required. This new approach to ASM drives continuous improvement and supports a sustainable company-wide culture of reliability.
“Reliability is a hard thing to embed in the culture of an organization, but having clear accountability and a system that supports that has helped us move towards best practice,” said Andrew.
The Challenge
- As a regulated utility, Icon Water needed to demonstrate leading practice asset management.
- Icon Water relied heavily on employee knowledge for maintenance, the “reason why and frequency ” of maintenance actions were not always documented.
- It had a short timeframe to develop strategies and package work orders to load into its new EAM
The Solution
- Consulting support from ARMS Reliability to help revolutionize Icon Water’s approach to Asset Strategy Management (ASM), tapping into 20+ years of Reliability expertise and using proven methodology and approach for immediate impact and fast delivery of project deliverables
- Access to one of the industry’s largest component strategy library, built up from +20 years of domain knowledge and failure mode data for faster and best in class strategy development
- OnePM rule-based maintenance plan grouping engine to ensure Master Data is consistently and automatically grouped into approved structures in alignment with Oracle EAM system and Icon Water standards
- Post implementation support to help Icon Water realize maximum value and continue to build team capability and a culture of Reliability
- Asset type, Reliability strategies built from first principles that support ongoing improvement and evolution of Icon Water’s asset reliability intelligence
Results
- Asset Strategy failure modes and control actions were developed for all asset types in Icon Water in 14 weeks, 90% faster than spreadsheets (total of 700,000 assets)
- Efficient Master Data generation with 20,000 work orders or activities loaded to the WAM
- Strong accountability of asset strategies to drive reliability
- Technical and content foundation for continuous reliability and performance improvement
- All work orders “re-packed” to increase delivery crew efficiency
- Annual Programme of work published to improve stakeholder engagement
- Leading Practice approach meeting with ISO 55000
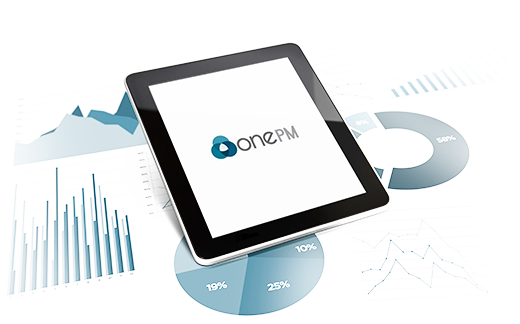
Discover OnePM
OnePM supports the process of Asset Strategy Management to deliver the optimal balance of cost, risk, and performance - continuously.
Learn How