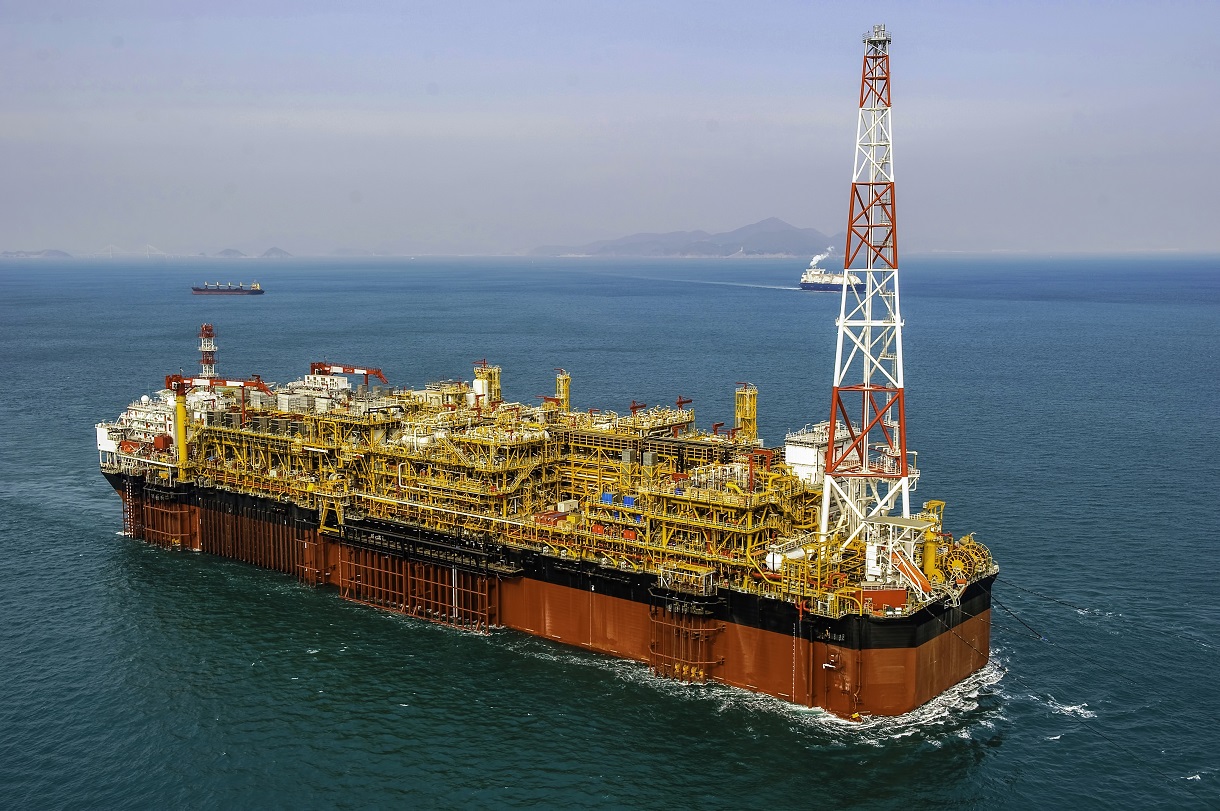
PROBLEM
A leading Canadian oil & gas company had an offshore operation that was spending 50 percent more on maintenance than other company platforms in the same basin. Additionally, the Floating Production, Storage, and Offloading (FPSO) unit was approaching the end of its 20-year design life – a period agreed upon with its governing body, the Canadian-Newfoundland & Labrador Offshore Petroleum Board (C-NLOPB). The oil & gas company needed help to determine the necessary maintenance to continue production using its existing equipment, while complying with C-NLOPB requirements, and minimizing both cost and risk.
The company also needed maintenance strategies that would provide:
- information it could give the C-NLOPB in order to renew the unit’s operating permit;
- a way to compare the operation’s current maintenance practices with recommended maintenance practices;
- the capability to forecast the operation’s resource requirements with timeliness and accuracy; and
- the ability to operate the unit at lower costs, comparable to its other platforms in the same basin.
Additionally, the company planned to adjust resourcing levels to more accurately fit new activity levels from ARMS Reliability’s forecast.
If the oil & gas company continued operation of the unit without optimizing its maintenance strategies, it risked loss of primary containments, leaks, spills, environmental hazards, rising maintenance costs, and continual breakdowns at huge costs due to the unit’s remote location.
SOLUTIONS
The oil & gas company selected ARMS Reliability’s OnePM®-powered ASM approach to identify the unit’s current maintenance gaps, develop optimized maintenance strategies for almost 48,000 assets, and standardize strategies across similar equipment.
The client chose ARMS Reliability based upon its technical expertise and proven experience optimizing maintenance strategies on projects in the oil & gas and petrochemical industries. Using the OnePM® solution for maintenance-task development has been demonstrated to be 3-4x more efficient than traditional approaches, and ensures operating context is considered in failure-mode mitigation.
Over a six-month period, the ARMS team used OnePM® to review and develop strategies for the unit’s almost 48,000 maintainable assets. Since all facilitations had to be performed remotely, the client-ARMS time-zone difference of 2.5 hours meant collaborative efforts had to be especially deliberate and well-organized. ARMS provided the client team with access to OnePM® so that they could watch the whole maintenance-build process in real time, and monitor strategy quality as each was completed.
Stage 1: Asset Strategy Preparation
Finding and Filling Maintenance Data Gaps
ARMS Reliability critically reviewed the client’s asset list and work-order history to identify gaps – such as incorrect grouping assignments, missing criticality values, naming inconsistencies, availability of OEM manuals, Bills of Materials, incorrectly assigned work orders, and blank fields – which might present challenges to delivering a successful outcome for the project. While ARMS’ ASM process is flexible towards data deficiencies, better-quality data typically produces a higher-quality solution. So, the ARMS team and the client team worked together to fill data gaps as much as possible, using practiced knowledge of industry best practices as necessary.
Stage 2: Asset Information Analysis
Developing Maintenance Strategy Recommendations
Based upon the updated asset information, ARMS Reliability leveraged its own asset-strategy library of Failure Mode and Effects Analysis (FMEA) templates to develop failure modes and mitigating tasks for each equipment sub-class. Using OnePM®, the ARMS team deployed the sub-class strategies to specific assets and, based on operational context, made necessary adjustments to the effects of failure, maintenance tasks, and sparing strategy, in order to maximize cost and risk effectiveness.
Using OnePM® access to view live progress, the client team reviewed ARMS recommendations and offered their own site-specific operational context. Facilitated workshops provided a platform to work through the ultimate changes to the process.
The ARMS team performed a detailed cost-benefit analysis on specified assets, to identify cost-effective and risk-mitigating maintenance tasks. For each failure mode, the cost, safety, environment, and other risk categories were forecast over a desired lifecycle, to determine the best maintenance strategy.
Once the optimized tactics and maintenance strategy were selected, ARMS performed a system forecast to define appropriate budget and resource predictions for the plan.
Stage 3: Equipment Strategy Approval
Consolidating Data and Recommendations for Optimal Strategy Data Sheets
Throughout this process, ARMS Reliability used OnePM® to merge grouped asset data with approved maintenance recommendations, simplifying the work required in this stage as custom views are made available to review and facilitate the consolidated strategy data sheets.
Before generating the strategy data sheets, OnePM® conducted an automated Quality Assurance (QA) check using defined rules developed throughout the project – including checks for blank fields and data inconsistencies that might compromise the quality of the strategy data sheets. Once the QA check was cleared and the data was approved, OnePM®’s report generator exported it all into the client’s strategy data sheets.
This superior method ensures generation of strategy data sheets is rapid, accurate, and responsive if further changes are required, negating the need to completely rework documents.
BENEFITS
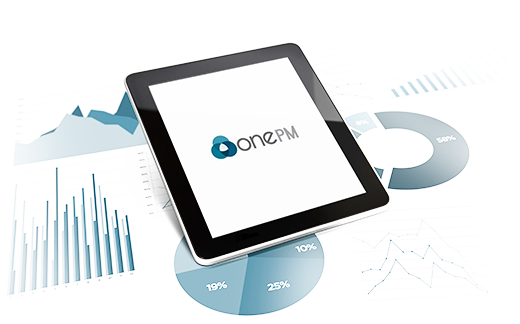
Discover OnePM
OnePM® supports the process of Asset Strategy Management to deliver the optimal balance of cost, risk and performance, continuously.
Learn How