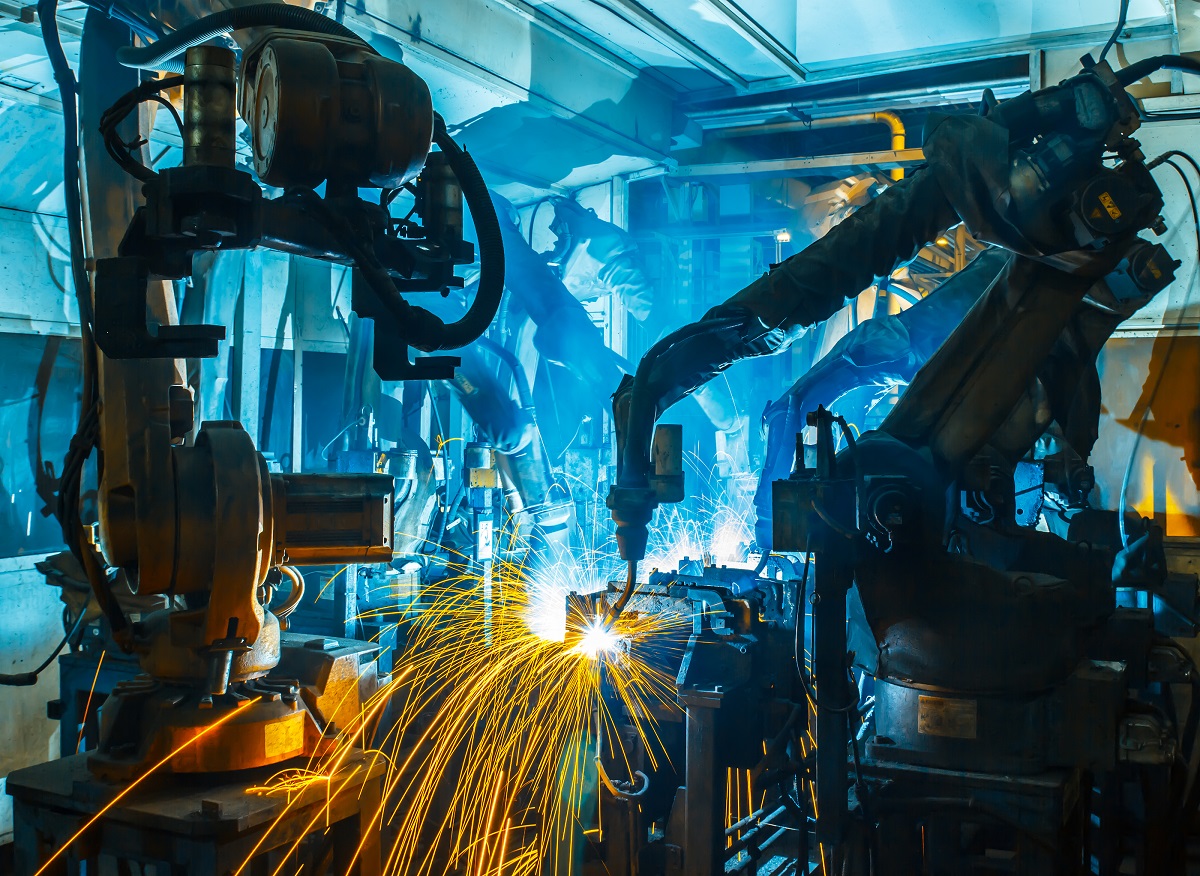
A manufacturer of heavy machinery was being crippled by excessive maintenance costs and continual disruptions on the production line. One of the culprits was the submerged (or sub) arc welding machine - which was failing on a regular basis.
A reliability study was performed on the machine, and it soon became clear that the manufacturer could reduce costs by up to 64%, or $139,886 per year.
The Problem
This company produces dump trucks for the mining industry. With an annual turnover of $11.7 million globally, it is a major player in the manufacturing industry - and has a tightly scheduled production line to cope with ongoing demand.
A key piece of equipment on this production line is the sub arc welder, which is used to weld structural beams for the chassis frame. Yet the sub arc welder was continually failing - leading to lost production, issues with quality and an excess of scrap product. The company commissioned a reliability study that was geared towards creating an optimized strategy for maintenance, and thus improving the ongoing performance of the welder.
The Solution
The company engaged ARMS Reliability to perform the reliability study.
Using reliability simulation software, a Reliability Centered Maintenance (RCM) model was built. As part of this, a Failure Modes Effects and Criticality Analysis (FMECA) was performed to identify all the likely and dominant failure modes, along with the effects of the failures.
The model was then run through a simulation to determine the benefit of each maintenance task on the equipment lifecycle costs and risk levels. It also revealed the criticality of each of the failure modes, so that maintenance tasks to mitigate each of the failure modes could be reviewed and optimized to improve reliability and reduce costs.
Further optimization and 'what if' scenarios were run, highlighting opportunities for redesign and further improvement.
Why perform an RCM study?
The RCM study delivered a number of tangible benefits for the company:
Accurate evaluation of scenarios
Reliability simulation software enables the simulation of different maintenance scenarios (e.g. run to fail, preventative or condition based), and compares these to the current practice.
Informed decision making
Armed with the accurate results from the study, the company could make decisions based on data rather than 'gut feel'.
Hidden failure costs are identified
The simulation takes all costs of a maintenance strategy into account, including the 'hidden' costs such as lost production, safety or environmental risks, asset damage, and reputation.
Highlights cost driving failure modes
The study reveals those failure modes that might not be obvious, yet are high cost drivers (e.g. high frequency of occurrence / short duration).
The Outcome
From the study, an optimized maintenance plan was produced. This plan was predicted to reduce costs by $139,886 (64% compared to current practice) per year.
In addition, an annual maintenance budget prediction (labor and spares costs) for the sub arc welding machine over its lifetime was produced. Significantly, the study highlighted a particular failure mode - welding tip damage - which was previously underestimated, as it is a 'short duration, high frequency' problem. This failure mode was actually the largest contributor to cost over the lifetime of the sub arc welding machine, due to production losses and quality issues. By addressing this problem, the company experienced significant savings.
Overall, the investment in a reliability study for maintenance optimization reaped huge rewards for the company - and this was just for one piece of equipment on their production line.
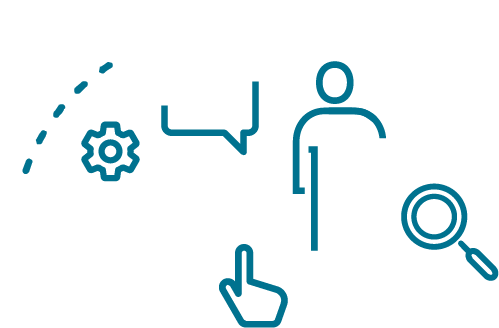
Questions? We’ll put you on the right path.
Ask about our Maintenance Strategy Optimization services and technical solutions. We are ready to help.
Contact Us